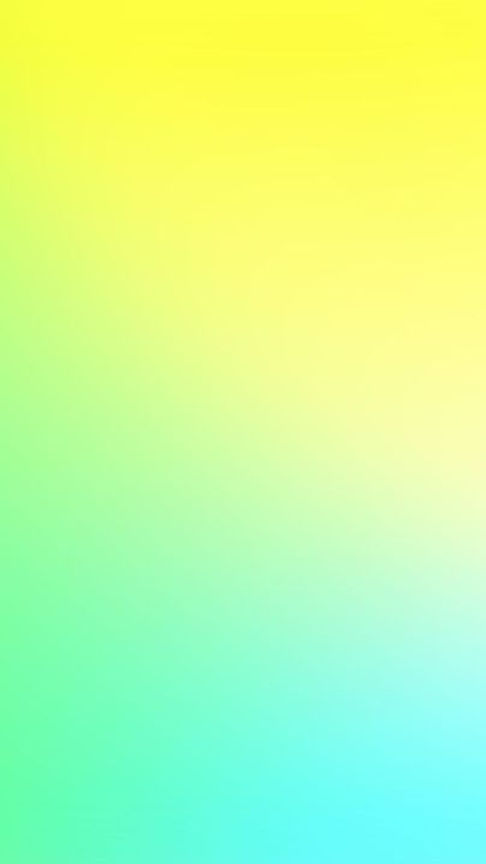
Extrusión :
Extrusión :
PROCESO DE EXTRUSIÓN
Para el estudio del proceso de extrusión es importante tener en cuenta los flujos existentes, los cuáles nos ayudan al movimiento de un material viscoso en el tornillo, estos se simplifican considerando tres tipos distintos de flujo:
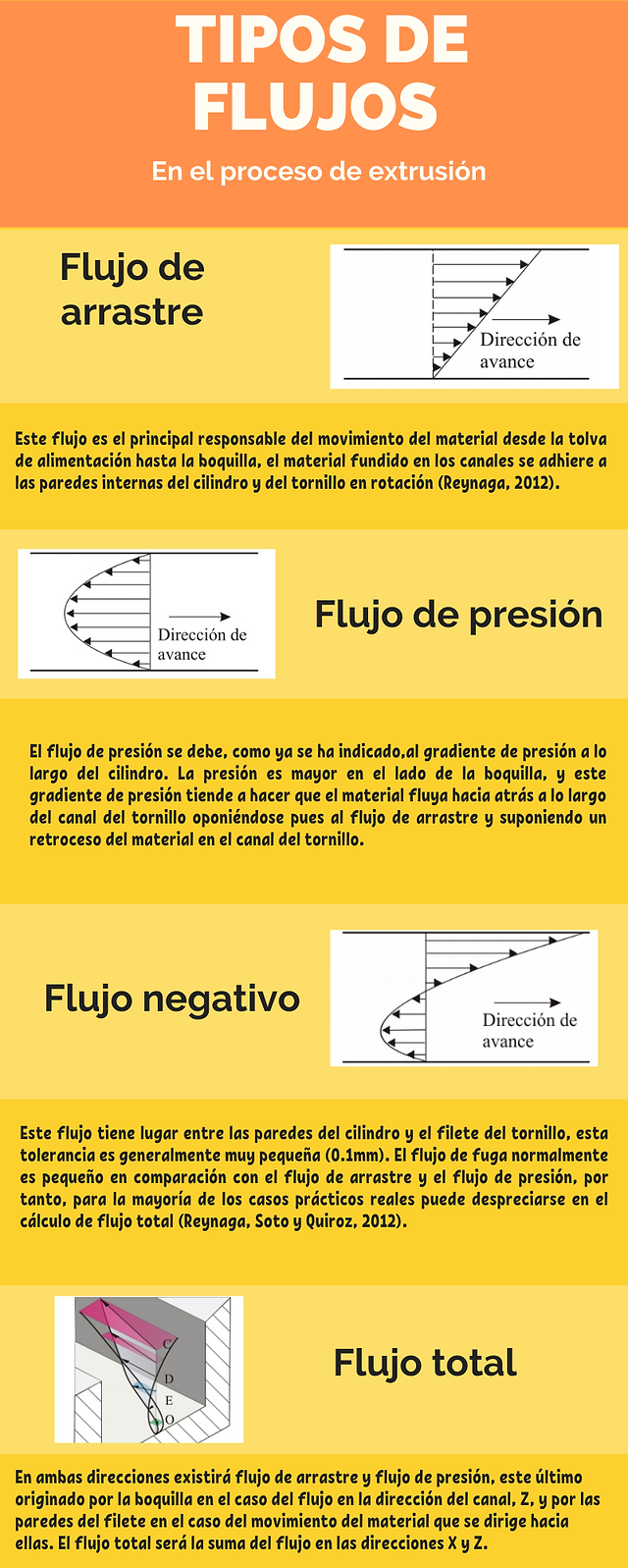
Existe una diferencia de temperatura en las zonas del proceso, debido a esto a continuación, se explica de manera detallada dónde y por qué se encuentra esta diferencia de temperatura.
DIFERENCIA DE TEMPERATURA EN CADA UNA DE LAS ZONAS
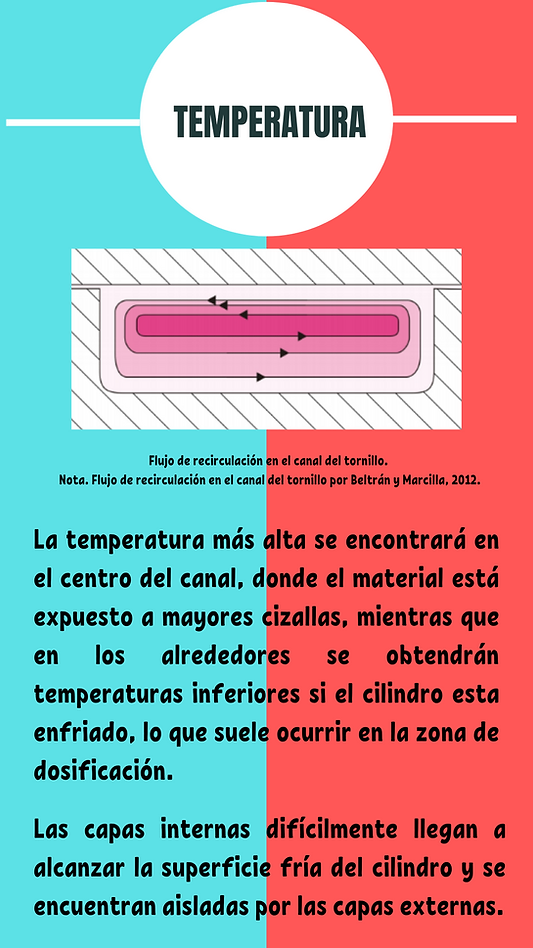
Una vez analizado los flujos que influyen en el proceso de extrusión, se explicará cada una de las funciones que se realizan en este, las cuales son; transporte de sólidos (zona de alimentación), transporte de sólidos en el cilindro (zona de transición), cocción, moldeado y corte.
1. TRANSPORTE DE SÓLIDOS
(ZONA DE ALIMENTACIÓN)
El transporte de sólidos en la tolva es, en general, un flujo por gravedad de las partículas, pero se puede dar un flujo en masa como se representa en la siguiente figura, el cual nos ayuda a no tener regiones estancadas y todo el material se mueve hacia la salida.

Flujo del material en una tolva de alimentación.
Nota: Adaptado de transporte y cizallamiento del tornillo, por Beltrán y Marcilla, 2012.
Para el transporte de sólidos existen diferentes características que influyen las cuales son:

Si se manipulan materiales con 60% de la densidad real este fluirá con mayor rapidez.
Es importante manejar materiales con factor de compresibilidad bajo, es decir, que sufran un cambio pequeño en su densidad aparente al aplicarles presión.

2. TRANSPORTE DE SÓLIDOS
EN EL CILINDRO
Una vez que el material sólido cae al interior del canal de la extrusora, el mecanismo de transporte deja de estar controlado por la gravedad y se transforma en un transporte inducido por arrastre. Este tipo de flujo tiene lugar debajo de la tolva a lo largo del tornillo en una distancia relativamente corta, la fuerza de fricción en la superficie del cilindro es la que genera el movimiento de la masa sólida hacia la salida de la extrusora, mientras que la fuerza de fricción en la superficie del tornillo es la fuerza retardante.
¿CÓMO PODRÍAMOS AUMENTAR EL COEFICIENTE DE FRICCIÓN?
R=
Para aumentar el coeficiente de fricción con el cilindro podría disminuirse la temperatura de este o de la garganta de alimentación, otra posibilidad consiste en utilizar cilindros con superficies rugosas, esto es, empleando cilindros estriados. Para una misma caída de presión a lo largo de la máquina, el caudal obtenido con un cilindro estriado es mayor que el obtenido con uno liso, como se puede ver en la siguiente figura, en donde se observa la representación del caudal de salida frente a la presión, para los diferentes cilindros.

Se tiene que los cilindros estriados permiten utilizar materiales con pesos moleculares elevados y difíciles de transportar.
Representación del caudal de salida frente a la presión, para un cilindro liso y para uno estriado.
Nota. Adaptado de representación del caudal, por Beltrán y Marcilla, 2012.
Una vez analizado esto, podemos decir que, el diseño de la estrusora es importante, a continuación, se muestran los diferentes tornillos que existen:

De acuerdo con la tabla anterior, para tener una menor fricción en el tornillo, el filete debe ser simple, el ángulo y el radio de los flancos lo más grande posible (Beltrán y Marcilla, 2012).
De igual manera la fuerza de arrastre o fricción entre el material y la superficie interna es mayor a menor rotación del material junto con el tornillo. La relación de L/D en extrusores de un solo tornillo es muy importante, a mayor L/D mayor superficie de fricción, que a su vez significa mejor propulsión hacia adelante bajo las mismas condiciones de extrusión (Reynaga, 2012).
3. COCCIÓN
La zona de transporte de sólidos finaliza cuando empieza a formarse una fina película de polímero fundido. La función se iniciará como consecuencia del calor conducido desde la superficie del cilindro y del generado por fricción a lo largo de las superficies del cilindro y del tornillo. Se genera gran cantidad de calor por fricción, de modo que, en ocasiones, es incluso posible iniciar la fusión sin necesidad de aplicar calor externo.
_.png)
Como ya vimos antes el proceso de cocción puede darse aunque no se haya suministrado calor, pero si queremos realizar un proceso de extrusión en caliente, el calor necesario puede ser suministrado por conducción desde la superficie caliente del cilindro, a través de la película fundida o bien por disipación viscosa debido a las fuertes cizallas a que está sometida la delgada película de fundido.
RECORDATORIO:
La conducción es el mecanismo de transferencia de calor en escala atómica a través de la materia por actividad molecular, debido al choque de unas moléculas con otras, donde las partículas mas energéticas, produciéndose un flujo de calor desde las temperaturas mas altas a las mas bajas.
Los mejores conductores de calor son los metales.

Esquema de los mecanismos de transferencia de calor.
Nota. Adaptado de Esque de los mecanismos de transferencia de calor por Conesa, 2013.
El flujo de calor por disipación viscosa esta favorecido al aumentar la velocidad del tornillo. Sin embargo, en este caso la contribución de la transmisión de calor por conducción a la fusión se verá reducida puesto que aumentará el caudal, y por tanto disminuirá el tiempo de residencia del material en la extrusora.
Un aumento de la temperatura del cilindro implicará en un principio un aumento del flujo de calor por conducción, y por tanto un aumento de la velocidad de fusión, pero por otra parte al aumentar la temperatura disminuirá la viscosidad del material y, por tanto, la generación de calor por disipación viscosa, de modo que algunos polímeros cuya viscosidad es sensible a la temperatura podrían ver reducida la velocidad de fusión.
¿QUÉ TEMPERATURA SERÁ LA CORRECTA PARA AUMENTAR EL FLUJO DE CALOR Y A SU VEZ CUIDAR LAS PROPIEDADES DE LA MATERIA PRIMA?
Existe una relación entre la longitud de fusión y la temperatura del cilindro para una velocidad constante, a continuación , se presenta una gráfica la cual nos explica esta relación.
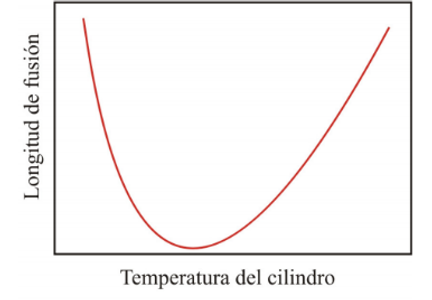
Relación entre la longitud de fusión y la temperatura del cilindro para una velocidad del tornillo constante.
Nota. Adaptado de relación entre la longitud y la temperatura, por Beltrán y Marcilla, 2012.
Se pude mostrar que se obtendrá una mayor longitud de fusión con una temperatura menor del cilindro, lo que nos indica que será mayor el tiempo de residencia ya que el material se fundirá de manera correcta y de igual manera estaremos cuidando las propiedades de nuestra materia prima, viendo el otro punto de la gráfica, donde se tiene una temperatura elevada del cilindro, obtendremos una longitud de fusión mayor pero el daño en nuestra materia prima puede llegar a ser irreversible.
Además de las condiciones de operación, la configuración del tornillo afecta en gran medida a la velocidad de fusión y a la longitud de fusión. El ángulo del filete del tornillo puede tener un efecto considerable sobre la eficiencia de la fusión, esto se puede mostrar en la siguiente figura.

Efecto del ángulo de hélice y del número de filetes sobre la longitud de fusión
Nota. Adaptado de efecto del ángulo, por Beltrán y Marcilla, 2012.
La longitud de fusión disminuye al aumentar el ángulo del filete. La eficiencia sería máxima con un ángulo de 90°, sin embargo, en este caso no se produciría el avance del material a lo largo de la máquina. Por tanto, hay que buscar ángulos que den buena eficiencia para la fusión y un buen transporte del material, normalmente se utilizan ángulos entre 20 y 30°; de igual forma como se vio anteriormente el tipo de filete influye teniendo que, con un filete sencillo se obtendrá una mayor longitud de fusión en comparación al doble y al de triple.
4. MOLDEO Y CORTE.
La boquilla es frecuentemente responsable de desarrollar la forma del producto. Sin embargo, una serie de deformaciones que se llevan a cabo mientras el producto fluido reacciona a su nuevo ambiente; cese del esfuerzo de corte, reducción de la presión y enfriamiento.
A continuación, se describe el proceso para dar el conformado del material:
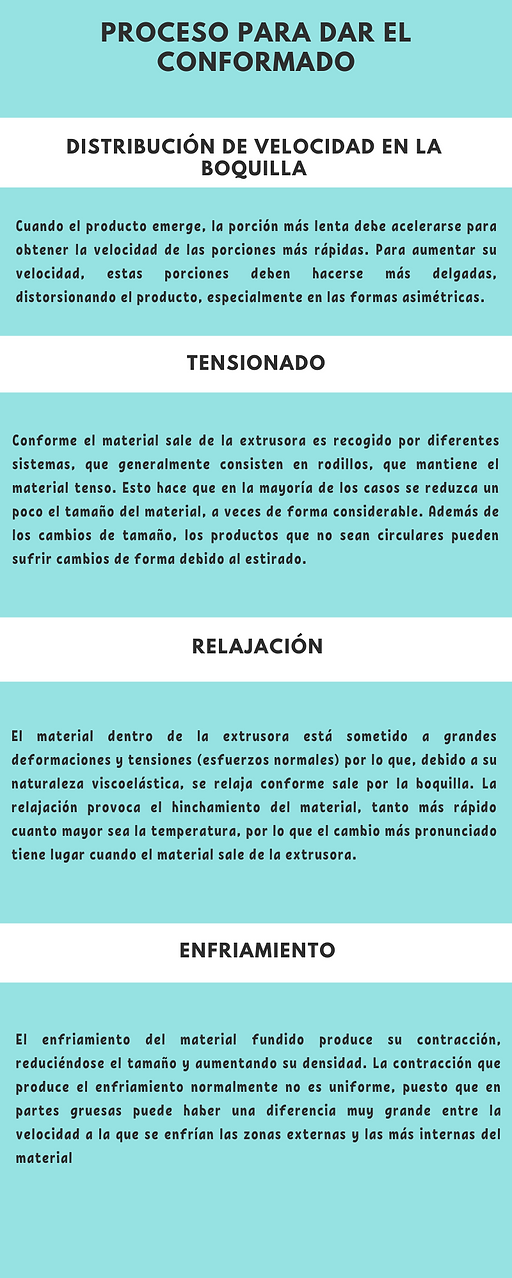
Esto también ocurre debido al cambio de presión entre la cámara del barril y la presión atmosférica, se produce una vaporización instantánea, y obtenemos un producto expandido con estructura porosa, que dependerá de las condiciones de funcionamiento y la composición de la mezcla, entre otros factores (Ruiz, Sánchez y Quintero, 2017).

Hinchamiento debido a la relajación de un material de sección cuadrada.
Nota. Adatado de hinchamiento debido a la relajación de un material por Beltrán y Marcilla, 2012.

Contracción debida al enfriamiento de un material de sección cuadrada. Nota. Adaptado de contracción debida al enfriamiento de un material por Beltrán y Marcilla, 2012.